Линия для обработки орехов фундука
Модель | TZ-10 |
Мощность | 13.1кВт |
Производительность | 250-300кг/ч |
Испарение | 70-90кг/ч |
Потребление природного газа | 5м³/ч |
Потребление сжиженного газа | 3.5кг/ч |
Теперь вы можете спросить наших менеджеров проектов о технических деталях
Линия для раскалывания орехов фундука — это современная производственная система, специально разработанная для раскалывания орехов фундука. Путем бесшовной интеграции ключевых компонентов, таких как подъемная машина, машина для открытия орехов фундука и конвейер для выгрузки, эта производственная линия достигает эффективного и автоматизированного рабочего процесса обработки орехов фундука.
От подъема сырых орехов фундука до точного открытия скорлупы и плавной транспортировки к последующим этапам обработки, линия для открытия орехов фундука не только повышает производственную эффективность, но и снижает затраты на рабочую силу, обеспечивая выдающуюся продуктивность и улучшение качества в отрасли обработки орехов фундука.
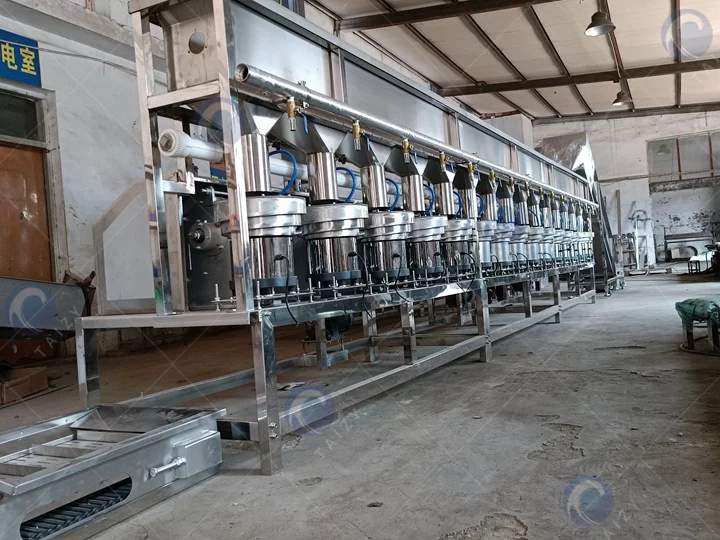
Ключевые преимущества линии по обработке фундука
- Точность раскалывания: Машина для раскалывания орехов фундука в линии обработки спроектирована с высокой точностью, обеспечивая чистое и эффективное раскалывание скорлупы орехов фундука. Эта точность минимизирует отходы и увеличивает выход целых ядер орехов фундука.
- Согласованное качество: Автоматизация и точность в линии обработки способствуют согласованному качеству в каждой партии. Это необходимо для соблюдения стандартов качества и обеспечения соответствия конечного продукта ожиданиям потребителей.
- Индивидуализация и гибкость: Линия для раскалывания орехов фундука часто разрабатывается с учетом гибкости, позволяя регулировки для учета различных сортов, размеров и требований к обработке орехов фундука. Эта адаптивность делает линию подходящей для различных производственных сценариев.
- Улучшенная безопасность пищевых продуктов: Линия обработки спроектирована с учетом стандартов безопасности пищевых продуктов. Автоматизированные процессы снижают вероятность загрязнения, а материалы оборудования часто выбираются за их гигиенические свойства, обеспечивая безопасность конечных продуктов из орехов фундука.
- Интегрированный поток процессов: Линия для раскалывания орехов фундука обычно интегрирована с другим оборудованием, таким как машины для сортировки, мойки, сушки и упаковки. Этот интегрированный подход обеспечивает бесшовный и эффективный поток орехов фундука через весь производственный процесс.
- Экономически эффективная работа: Хотя первоначальные инвестиции в настройку линии обработки могут быть значительными, ее экономическая эффективность становится очевидной со временем благодаря повышению эффективности, снижению затрат на рабочую силу и минимизации отходов.
- Конкурентоспособность на рынке: Согласованное качество, эффективность и автоматизация линии для раскалывания орехов фундука способствуют конкурентоспособности обработанных орехов фундука на рынке, соответствуя ожиданиям потребителей и стандартам отрасли.
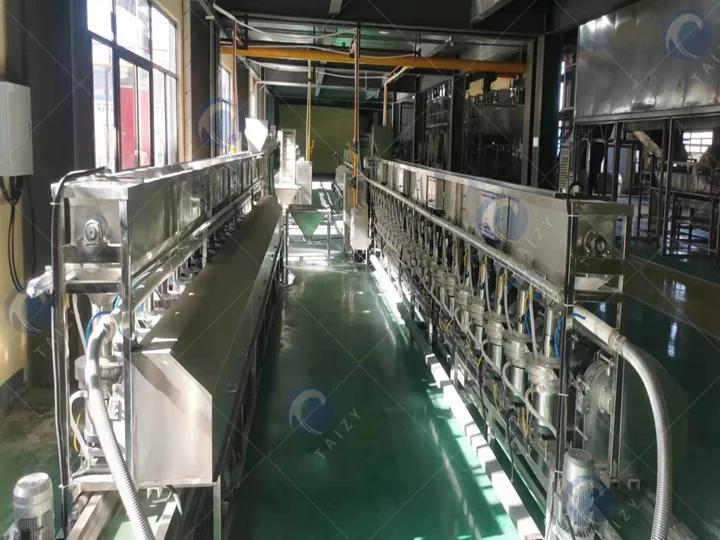
Принцип работы линии по обработке фундука
Сначала орехи фундука замачиваются в теплой воде при температуре около 50 градусов в течение 30 минут, чтобы смягчить скорлупу. Затем орехи фундука помещаются в подъемную машину, попадая в накопительный бункер с винтовым конвейером, который равномерно распределяет их по различным каналам. Производственная линия оснащена парогенератором, который производит пар в каналах. В конце каналов две пресс-плиты достигают эффекта раскалывания за счет сжатия. Расколотые орехи фундука автоматически падают на конвейер ниже.
Расколотые орехи фундука могут по желанию перейти к следующей сушильной машине для удаления избыточной влаги. Наконец, открытые и высушенные орехи фундука могут быть направлены к упаковочной машине для упаковки.
Вся производственная линия, благодаря последовательной серии процессов, осуществляет автоматическое открытие и начальную обработку орехов фундука, повышая производственную эффективность. Кроме того, гибкость линии позволяет включать такие этапы, как сушка и упаковка, в зависимости от конкретных требований.
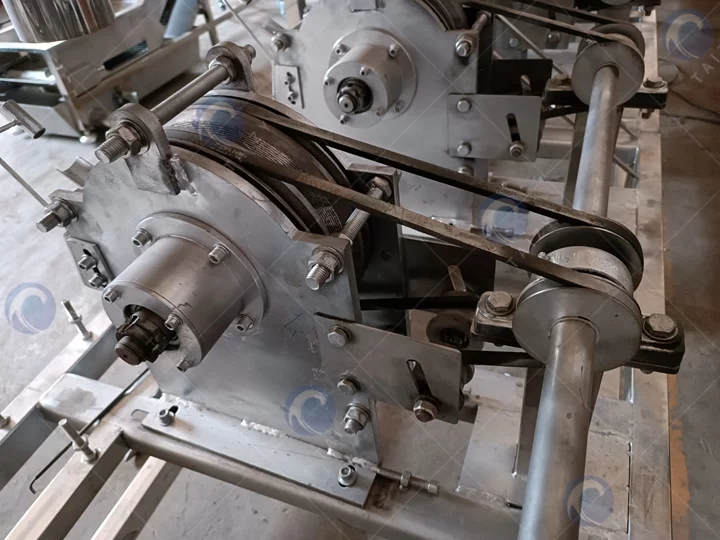
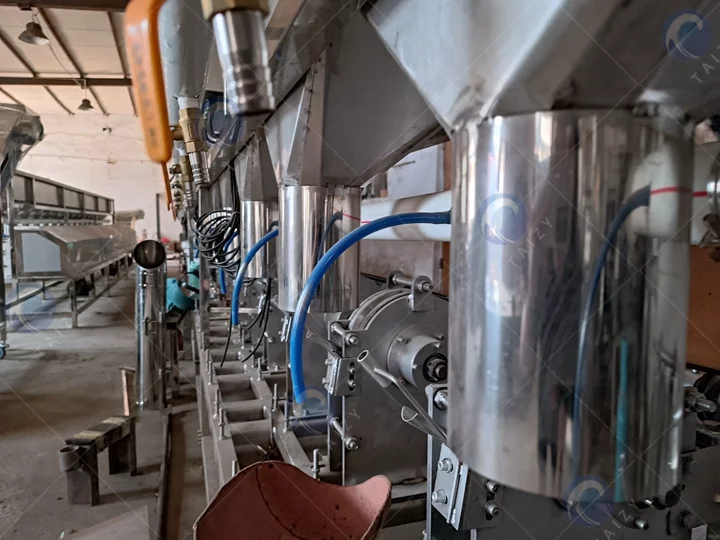
Рабочее видео линии по обработке фундука
Оборудование для поддержки линии по обработке фундука
1. Ёмкость для замачивания
Бак для замачивания является ключевым компонентом линии для раскалывания орехов фундука, обладая функцией нагрева. Эта машина предназначена для замачивания орехов фундука перед их поступлением в линию обработки. Процесс замачивания направлен на смягчение скорлупы, что облегчает открытие орехов фундука.
Солильный бак обычно оснащен системой контроля температуры, позволяющей регулировать температуру воды для обеспечения идеальной среды для замачивания. Это способствует улучшению эффекта трещин и создает оптимальные условия для последующих этапов обработки.
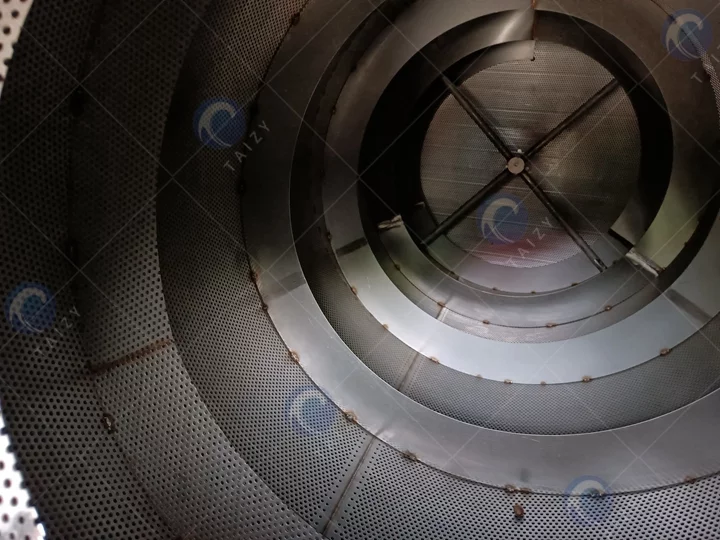
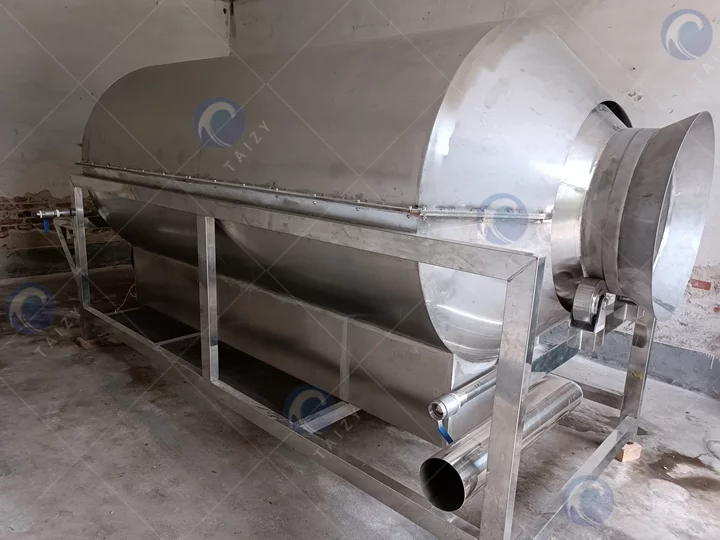
2. Сушильная машина
Сушильная машина является одним из вспомогательных устройств в линии обработки фундука. После того как фундук прошел процесс трещин и первичной обработки, сушильная машина используется для удаления избыточной поверхностной влаги, улучшая качество и текстуру фундука.
Эта машина использует горячий воздух, чтобы обеспечить достижение фундуком желаемого содержания влаги. Использование сушильной машины помогает продлить срок хранения фундука, предотвращает рост плесени и улучшает общее качество конечного продукта.
3. Упаковочная машина
Упаковочная машина является конечным оборудованием в линии обработки фундука и отвечает за упаковку открытого и высушенного фундука. Упаковочные машины разработаны с высоким уровнем автоматизации и гибкости, чтобы соответствовать различным спецификациям и требованиям к упаковке.
Эффективная упаковка помогает обеспечить сохранность и гигиеничность фундука во время хранения и транспортировки, что в конечном итоге повышает конкурентоспособность продукта на рынке.

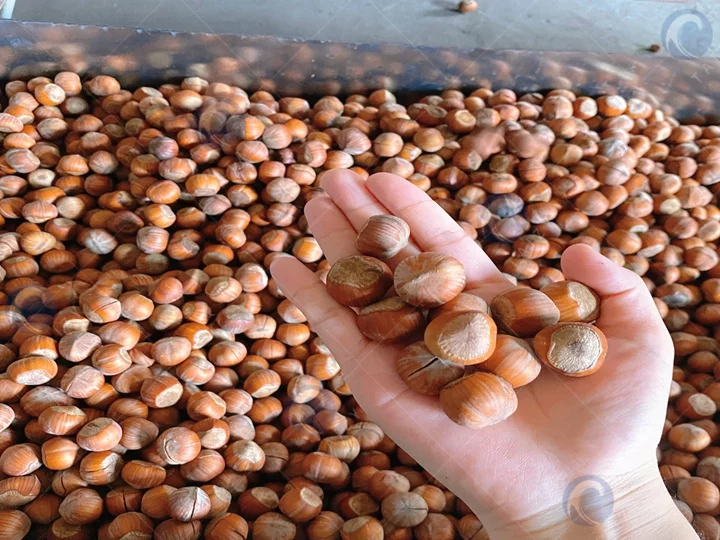
Технические параметры линии по обработке фундука
Наша линия обработки фундука доступна в различных мощностях, предоставляя гибкость выбора в соответствии с конкретными производственными требованиями. Эта адаптивность позволяет настраивать оборудование в зависимости от масштаба операций и желаемого выхода.
Разные варианты мощности отвечают различным производственным потребностям, обеспечивая, что наша линия обработки может эффективно удовлетворять требования различных масштабов обработки фундука. Независимо от того, для небольших операций или для крупного промышленного производства, наша линия обработки фундука предлагает универсальные решения для удовлетворения разнообразных производственных нужд.
Модель | Производительность | Мощность | Испарение | Потребление природного газа | Потребление сжиженного газа |
TZ-10 | 250-300кг/ч | 13.1кВт | 70-90кг/ч | 5м³/ч | 3.5кг/ч |
TZ-15 | 350-450кг/ч | 16кВт | 80-110кг/ч | 7м³/ч | 5кг/ч |
TZ-20 | 500-600кг/ч | 18кВт | 80-110кг/ч | 7м³/ч | 5кг/ч |
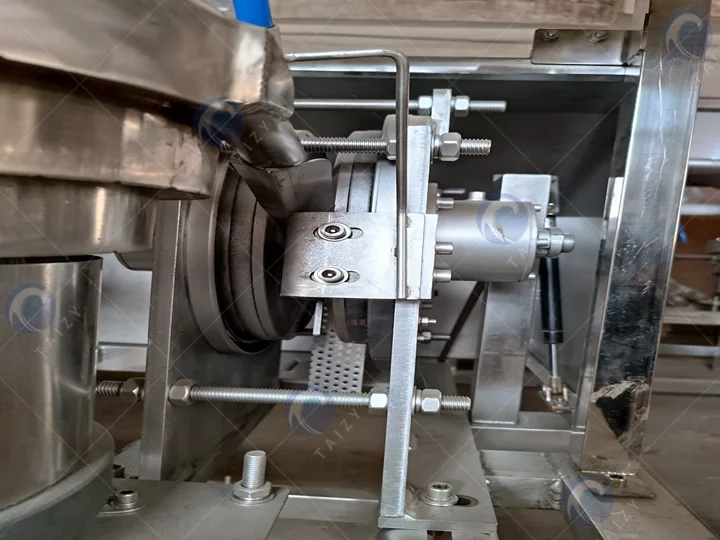